Conveyor Belt Tracking
Misaligned conveyor belts have the potential to cause many problems associated with the conveying of bulk materials. This includes material spillage and reduced life to conveyor belting and the conveyor structure.
Spillage poises safety hazards in the form of trips, slips, falls and entanglement as well as potential damage to idlers and roller seizures. When the conveyor belt moves off centre there is greater risk of conveyor belt edge and conveyor structural damage, all of which is costly in terms of replacement and production downtime to faciliate the installation.
A conveyor belt must run “True” to avoid material spillage at the transfer points and a conveyor belt must run “True” to avoid damage to the edge of the conveyor belt and conveyor components.
Conveyor belt misalignment can be result of a number of conditions: damaged conveyor structure or ill-fitting components, poor belt splices, environmental and material loading factors.
How to Prevent Conveyor Belt Mistracking
First the belt needs to be audited and problem areas identified. Next the idlers and pulleys should be aligned, so that correct loading in the centre of the belt can be achieved. Belt tracking devices should be installed to ensure that the belt remains level and “True” under all operating conditions. Ideally a pivoting, self-centralising, belt training system, which rotates freely when the belt experiences mistracking behaviour should be installed. Other options include fixed tracking solutions without rotating structure, plus an early warning support mechanism to cue safety drift misalignment.
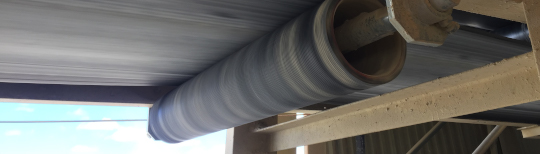